All our wheels come with a spoke pattern that suits the hole count and use of the wheelset.
Rim brake wheels, for example the Lark and Mahi-Mahi – We use radial lacing on many of our front rim brake wheels. Most of our rear road wheels now use a 2:1 spoke pattern, where there are twice as many spokes on the drive side as on the non-drive-side.
Disk brake wheels, including Traildog MTB and Map road-disk and Gecko gravel wheels. Disk brakes apply a rotational force between the hub and rim so a crossed spoke pattern is essential to resist this. We use 2 cross patterns on 24 and 28 hole hubs and 3 cross lacing on 32 hole hubs – these patterns end up with approximately equivalent spoke arangements, with parallel spoke pairs roughly on opposite sides of the hub, providing maximum resistance to rotation.
As we can build our wheels to order please contact us if you prefer a different pattern and we will try to help.
radial lacing
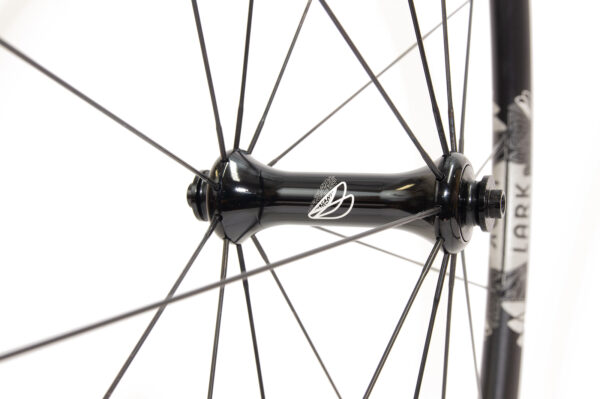
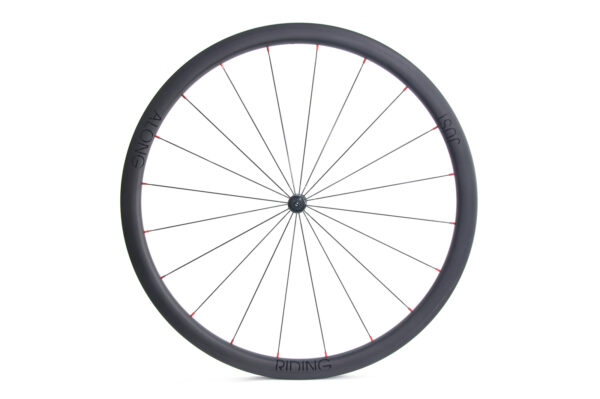
Radial lacing on both sides is for front rim brake wheels only as it does not transfer any braking or driving force from the hub to the rim. There is a small weight and aerodynamic advantage to be gained from using radial lacing as it has shorter spokes.
Two cross lacing
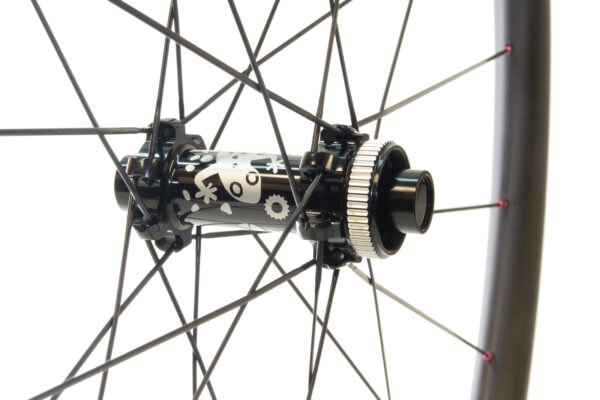
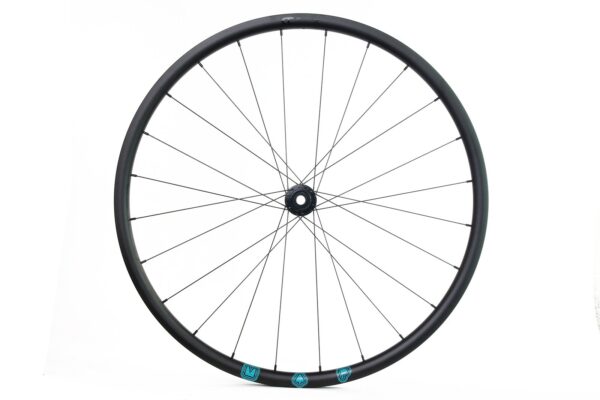
Two cross lacing is very similar to 3 cross but we use it on 24 and 28 spoke count wheels. The spoke crosses 2 other spokes between the hub and the rim.
Choosing the right lacing pattern ensures that the spoke enters the rim at the correct angle without stressing the rim or the nipple.
Three cross lacing
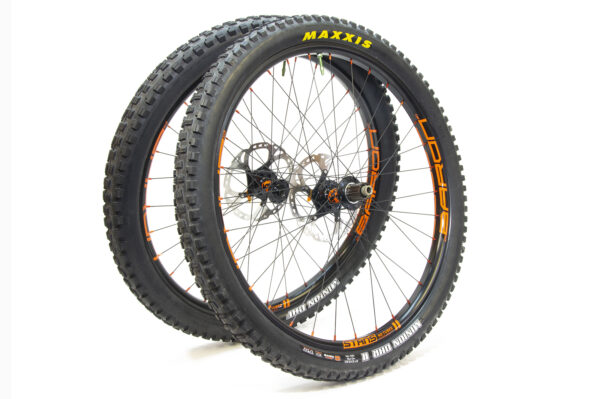
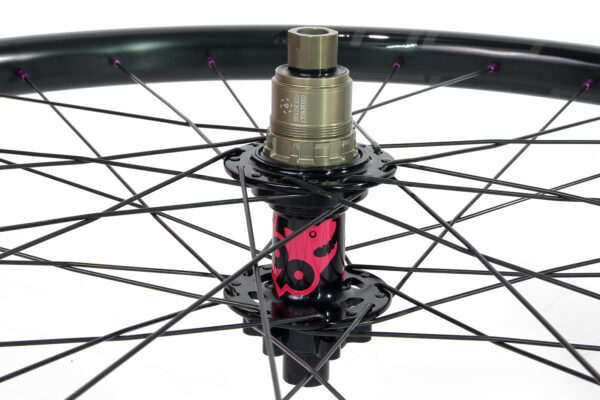
Three cross lacing pattern, for strength and durability on both rim and disk brake wheels with 32 spokes. The spoke crosses three other spokes between the hub and the rim, spokes facing the centre of the hub cross over two spokes before going under the third spoke to the rim.
2:1 spoke lacing pattern
This pattern is used on most of our road (rim brake) rear wheels, it allows us to build very strong wheels with relatively low spoke counts.
Road wheels built with standard-drilled hubs (same number of spokes on each side) usually have spoke tension on the drive side double the tension of the non-drive side due to the offset required for the freehub. By using twice as many spokes on the drive side as on the non-drive-side, the tensions are almost equal between the 2 sides.
This has many benefits:
Lower stress on the drive side: to achieve a good (high enough) spoke tension on the non-drive-side, the drive side spokes of a conventional drilled hub/rim must be at a very high tension, especially so since 11-speed came along with a longer freehub than 10-speed. This puts stress on the rim and hub potentially leading to cracking and distortion. With the 2:1 pattern both sides are at the same tension and a lower spoke tension can be used.
Non-drive-side spokes less likely to loosen: With spoke tensions on some wheels as low as 60kg on a standard drilled hub, the non-drive-side spokes are prone to loosening.
Low weight and/or increased strength of the wheel: a 24-hole hub in a 2:1 arrangement has 16 spokes on the drive side which is the same as a 32-spoke conventional wheel. A 27-spoke wheel (9/18 drilling) has the same number of drive side spokes as a 36-spoke conventional wheel! This makes it extremely strong.
We don’t use the 2:1 pattern on disk brake wheels. Because the rear wheel has a disk mount one side and freehub the other, there is less difference in the spoke tensions and going 2:1 would end up reversing the problem with higher spoke tensions on the non-drive-side. On some wheelsets we instead use an asymmetric rim (for example the Gecko) which evens up the spoke tension. On newer mountain bike wheels with Boost spaced hubs there is very little difference between the two sides anyway.